Comparison of Traditional Clamping and Permanent Magnetic Clamping
2024-11-7
The traditional clamping way is to fix the workpiece only by traditional tools such as clamping plate, vise, hydraulic (pneumatic) clamping tools etc. These clamping tools can cause damage and extrusion deformation to the surface of the workpiece. Certain clamping tools are too costly and not versatile enough. For example, hydraulic clamping tools.
Due to pressure point interference, machining always requires clamping several times, efficiency and machining accuracy greatly affected. Due to the point contact, the support surface is limited, the resonance will happen in the machining process, which affects the machining efficiency and tooling costs.
And the workpiece will generate rebound problems after machining. Cumbersome clamping is not only inefficient, but also labor-intensive. And how to reduce the consumption of electricity, liquid, gas and other energy? Safety issues due to mechanical strain? Batch processing waiting time? All of these are problems that need to be considered in actual machining production.
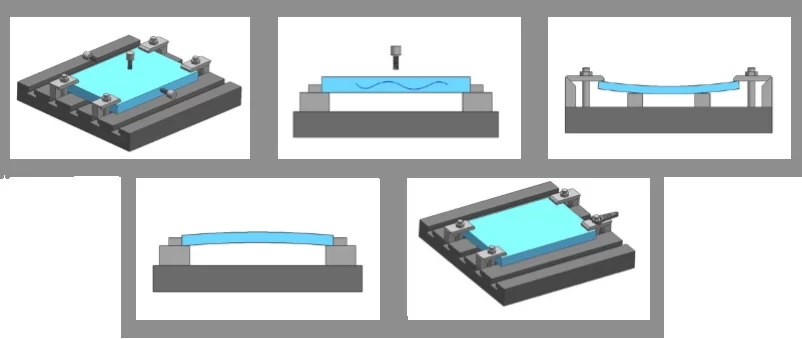
The above problems can be well solved by permanent magnetic chucks, magnetic clamping has the following advantages
1 No stress, no heat, no deformation clamping, high precision of finished products.
2 Reduce the resonance during machining and prolong tool life.
3 Once clamping can achieve five-sided machining without jamming.
4 Instant magnetization / demagnetization, when batch machining, greatly save the clamping, calibration time, equipment has high rate of moving.
5 No need to take care of the fixture's electricity, liquid, air line space, make full use of the equipment work platform.
6 With the magnetic block and magnetic plate, high versatility, reduce the repeated investment in work holding clamp tools.
7 One-control multi-mode, simple operation, effective reduction of labor costs Based on modular design, to meet the needs of flexible work.
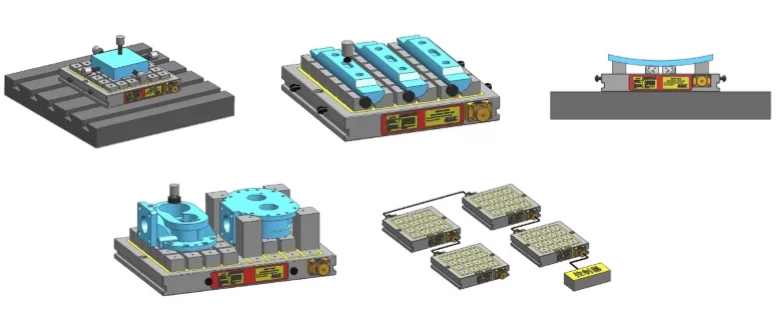